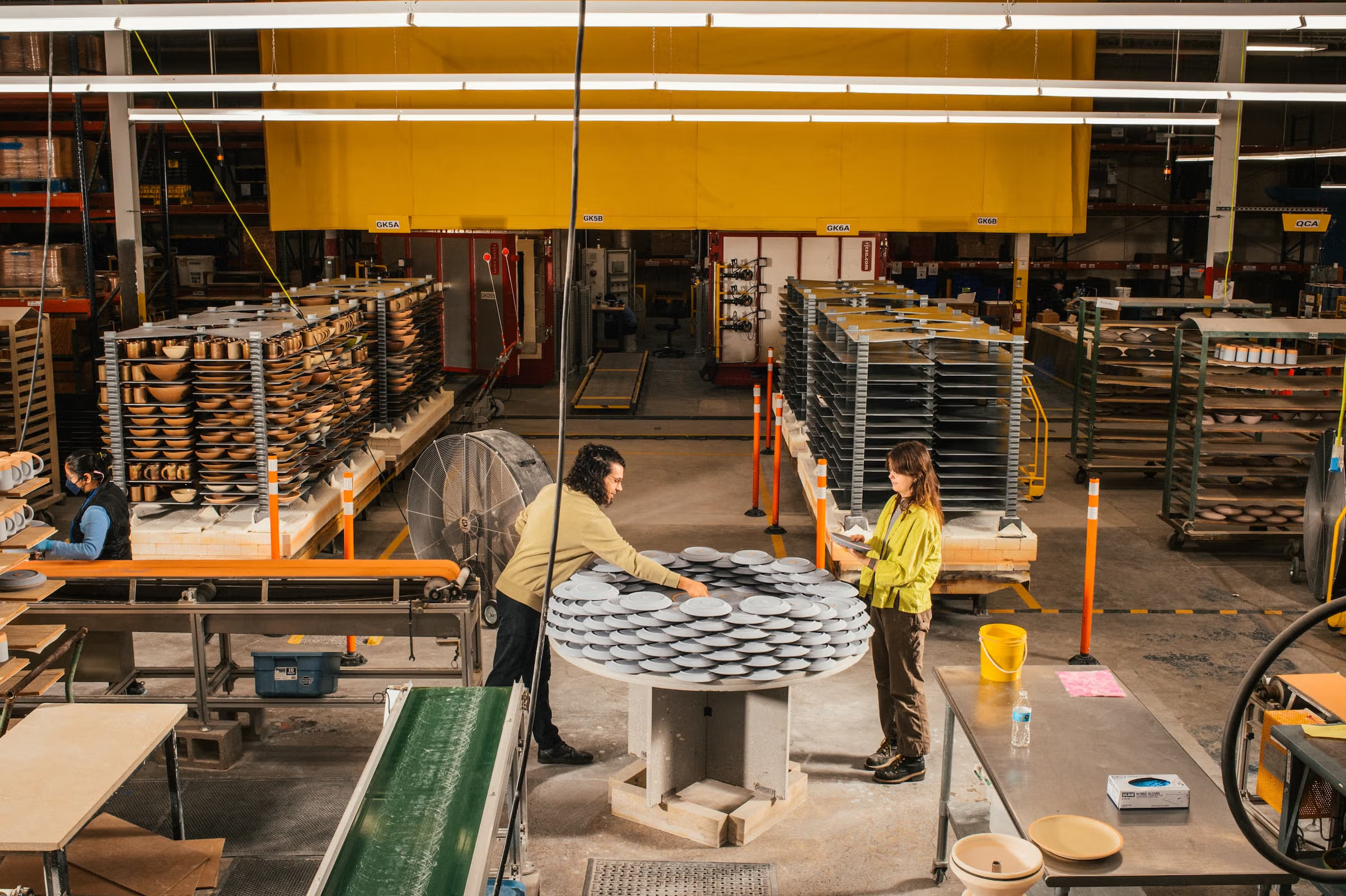
Update on How Our Pots Get Made
This post was last updated in July 2023.
We’re on the precipice of some large changes on the manufacturing floor as we prepare to move to a new clay body and glaze recipe. If you’ve been in the East Fork universe for a few years you’ve seen change before: when we switched from firing with wood to gas (the biggest change in our history!), the switch from our original clay to the clay we use today, and countless small changes in glazes textures and hues and the amounts of iron spots. As I say to our team: Change is the only constant.
These changes are the culmination of over 3 years of work to improve the quality of our materials, ensure our clay works on all of our new forming processes, address some major quality control issues, and in the case of our glaze react to the unexpected disappearance of a core material we use in our glaze formulas.
This is a huge moment for East Fork. I want to thank all the individuals who contributed to this work over the last few years. In particular I’d like to thank Devin McMillen and Sara Melosh who ran hundreds of tests and stayed focused on the prize to get this ambitious project over the finish line.
Our new clay will appear smoother and sometimes darker in color. There have always been slight variations from firing to firing because of the reduction process and these subtle variations will continue to exist. Our new clay should also improve the reliability of our iron spots from firing to firing, although in the beginning as we dial in our firing curves you may still see some variation from pot to pot. Some of the forms that we don’t have a lot of bisque inventory in will have a faster transition while others with deeper stocks of bisque inventory will take more time to begin flowing through the kilns.
The Clay
The clay we have used for the last 4 years had several issues we are solving with a redesign.
Particle Size - Our old clay was designed before we installed many of the industrial processes we use today. The clay that was mined in Georgia and had a very large particle size distribution… This means that the machinery has been running at rates that are much slower than its design intended. Our new clay with smaller particles will be able to run on all of our equipment, increasing our quality and efficiency, which in turn leads to more organizational stability and profitability.
Bloating - Currently, The clay we use has a very high bloating rate. Our kilns are designed to be run in a fully automatic fashion, however we need to manually fire the kilns through the end of the firing to reduce the bloating. The unintended effects of this are that as we reduce bloating we also reduce the iron spots in the clay and increase other issues.
Iron Spotting - Many customers have noticed more variation in the iron spotting of our pottery. Because of the manual firing process some firings have more iron spotting and some have less. Our new clay will bring less variation to the amount of iron spotting we see in our clay.
What are some of the differences we can expect to see from this new clay?
Color and Appearance - The new clay will have a smoother appearance than our current clay and the color will be more uniform with less variation in the surface. With our firing process we see variation in color of the clay and we will continue to have some slight variation in the color.
Texture and feel - Our new clay has much smaller particles so the texture of the clay will be much smoother than our current clay.
Quality - The new clay will continue to decrease our Seconds rate to our target of 80%. This brings more stability to our organization through better margin contribution and increased throughput on all of our processes.
The Glaze
We’ve switched our glaze formula because our current glaze contains Petalite: a mineral that contains lithium. As the battery industry has grown they have started to buy up all minerals containing lithium. First the price for any material containing lithium exploded, then the supply chain dried up completely. The disappearance of this mineral forced us to quickly switch formulas.
What changes can we expect to see with our new glaze?
Over the years our glazes have always shifted and changed slowly as we update formulas to increase our yield and improve the quality of the glaze. The switch to a new base glaze will bring some changes that will be subtle but noticeable to the discerning eye.
Texture - The texture of our glaze will become slightly smoother. Our current glaze has a very fine texture to it that we refer to as an orange peel. The new glaze will be a little smoother while retaining the matte qualities of our glaze.
Color - Each stain reacts differently in the base glaze. While some glazes like Panna Cotta, Eggshell, Black Mountain, and Amaro will remain very close to the original color, Morel and Blue Ridge may shift slightly. Overall you can expect to see colors that feel a little more saturated and rich.